Estratégias de Design Aditivo de Metal
Onde a forma segue a função para alcançar a redução dos componentes.

Por Colin Blain, Aplicações avançadas, 3D Systems.
Existem 3 estratégias de design chave que beneficiam peças que são fabricadas de forma aditiva – especialmente quando impressas em metal. Estas três são: a redução do peso das peças, a integração de características complexas difíceis e muitas vezes impossíveis de realizar de forma convencional, e finalmente, redução de componentes. Apesar da redução de componentes ser uma metodologia especifica no design, é mais bem-sucedida quando incorpora todas as metodologias de design simultaneamente.
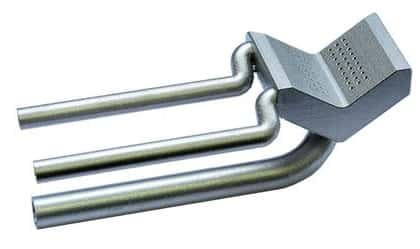
Redução de componentes, ou PCR, utiliza a manufatura aditiva, é uma abordagem nova de design que proporciona uma peça monolítica otimizada, substituindo uma peça que depende da montagem de vários componentes. Pesquisa, testes e implementação destas peças mostram que com uma metodologia correta, estas peças únicas consolidadas podem proporcionar melhorias de performance significativas, reduzir o peso dos produtos em geral, melhorar a durabilidade de produtos, um fabrico mais económico e consideravelmente mais rápido que métodos tradicionais, no entanto com mais complexidade e funcionalidades.
Apesar dos benefícios listados acima serem um ótimo começo, o PCR pode proporcionar vantagens adicionais que não estão sempre evidentes.
Redução no número de componentes remove a montagem de um processo. Nestas situações, o negócio reconhece imediatamente melhorias.
- Tempos de produção mais reduzidos;
- Tolerâncias melhoradas e eliminação do agrupamento de tolerâncias;
- Redução de custos relacionados com trabalho de montagem;
- Redução no custo de materiais;
- Redução do risco de uma montagem com erros;
- Menos inventário e peças em “contentores”;
- Redução potencial de custos de peças.
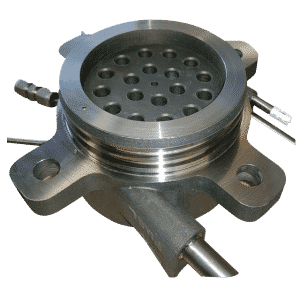
Quando tem uma peça consolidada, a sua linha de topo pode melhorar porque pode ter:
- Peças melhores que respondem ás necessidades dos seus clientes;
- Um design funcional mais eficiente;
- Uma cadeia de fornecimento mais fluida;
- Um processo de fabrico mais ágil;
- Tempos de lançamento para o mercado mais rápidos e o seu respetivo lucro.
Aqui está um ótimo exemplo: Recentemente pesquisamos um design para um escape para desportos motorizados para um cliente, na imagem abaixo, poderá ver cerca de 20 peças em chapa metálica necessárias para soldagem, incluindo vários componentes hidroformados, cada um precisa de maquinagem individual. No lado direito verificamos uma peça única, um escape consolidado produzido com impressão 3D de metal.
Esta peça foi impressa em apenas 23 horas utilizando titânio 23, comparado com as 3 ou mais semanas que seriam necessárias para produzir o escape tradicionalmente. Tempo de design deste escape foi reduzido de 6 semanas para 6 dias. A tecnologia aditiva também remove a necessidade de maquinagem, fixação, múltiplas soldagens e apenas precisa de algumas inspeções.
A otimização de geometria reduziu a quantidade de material necessária e ajuda a maximizar a performance. Todos os elementos do escape original são incorporados no novo design e quando impressos com a espessura convencional de 0.5mm, é aproximadamente 25% mais leve que o escape original.
Gostaria de ter acesso a mais conteúdos como este?
Subscreva a nossa newsletter e receba informação sobre novos artigos, oferta formativa, webinars, eventos, campanhas e muito mais!